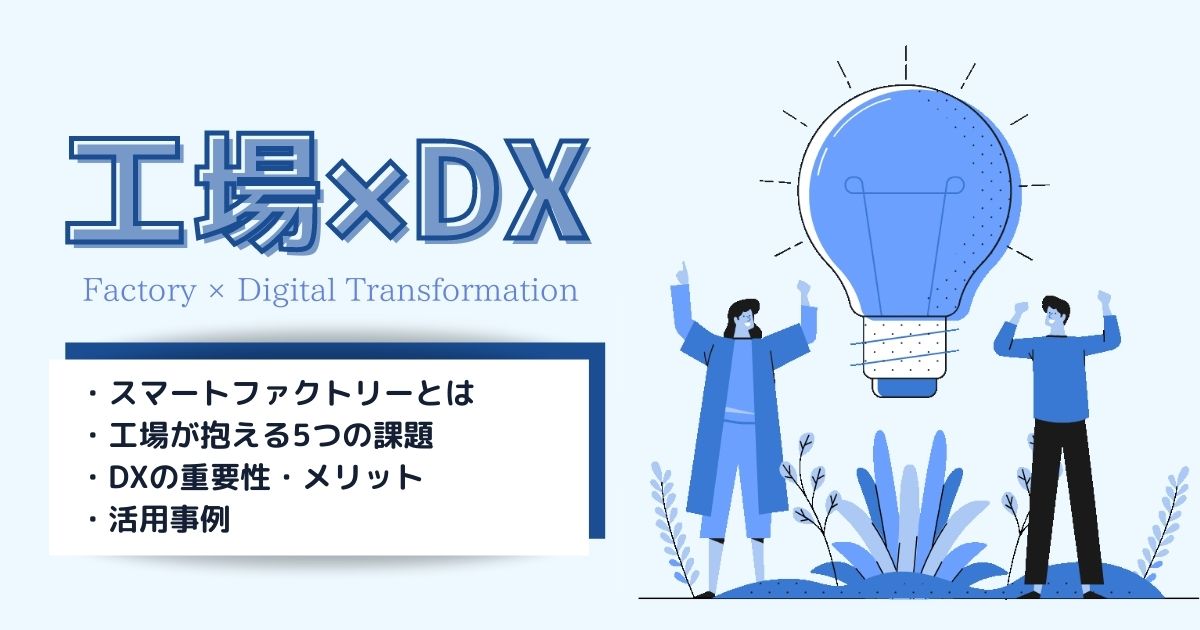
DXは、既存の業務システムやビジネスモデルを変革させます。そのため、今まで抱えていた課題の解決にも繋がるでしょう。
現在、人手不足を始めとした様々な課題を抱える工場があります。これらの課題がDXの推進によって解決され、更に生産性の工場を達成した事例もあります。
この記事では、工場におけるDXの推進について、現状の課題とDXの重要性やメリット、事例などを紹介します。是非、参考に取り入れてみてください!
目次 [非表示]
「DX」「スマートファクトリー」|用語の解説
DXとは?
DXとは、「デジタルトランスフォーメーション」の略であり、経済産業省によって発表された「DXレポート」で広く認知されるようになった概念です。DXの目的は、デジタル技術を用いて、ビジネスモデルや業務を改革し、最終的には組織自体の変革を成し遂げる事とされています。
▼DXの概要について詳しくはこちら
スマートファクトリーとは?
スマートファクトリーとは、IoTやAIなどの先進技術を用いてデジタルデータの活用・分析し、生産性向上のみならず、設計から製造までDXを実現する工場のことです。
ドイツ政府主導の国家プロジェクト「インダストリー4.0(第4次産業革命)」で提唱され、現在世界中で注目されている概念です。工場でDXを行うことで、同時にスマートファクトリー化が達成されます。
工場が抱える5つの課題
工場が抱える問題は以下の5つです。
それぞれ解説します。
①人材不足
昨今、すべての業界で課題となっているのが人材不足です。その中でも製造業では、少子高齢化による労働力人口の減少の煽りを受けるとともに、デジタルネイティブの若年層がIT産業に惹かれる傾向があります。
また、中小規模の製造業では、これまで職人・熟練技能者たちの専門的な知識や高度な技術によって支えられてきました。しかし、職人の高齢化と継承者不足によって、高い技術と知識を維持が難しくなっています。
このように、人材不足は技術継承の観点からも、非常に深刻な問題です。
②IT知識不足
日本は、世界に比べるとIT化が遅れているといわれています。製造業においても、新たにIT化せず老朽化した設備を使用し続けるメーカーもあるといいます。その要因として以下の4つが挙げられます。
①使いこなすための知識と技術を持った技術者が少ないこと ②コストの確保が難しいこと ③生産性の向上などIT化による効果が理解できていないこと ④IT化を進める目的が明確になっていないこと |
③技術力の継承
日本の製造業における技術力の高さは、世界的に評価されています。しかし上記にも述べたように、高度な技術をもつ職人たちも高齢化しています。
これらの技術は、技術者たちの経験と勘によって支えられてきたため、技術の継承には後継者が必要ですが、人材不足により後継者の確保が困難となっています。
④需要への対応
昨今、顧客のニーズに合わせた多品種少量生産が主流となりつつあります。更に需要の変動も激しく、生産や在庫の調整を誤ると過剰在庫や、逆に欠品による機会損失を招いてしまいます。
⑤生産性
工場では、現在でも紙の帳票などのアナログな業務があります。アナログな業務に人員が割かれることで、非効率的な運営となり、生産性も低迷します。
工場におけるDX推進の重要性と4つのメリット
重要性
工場でDXを推進することで、これらの問題を解消できます。少子高齢化となった現代において、人材不足は深刻な問題です。この危機を脱するには、既存のシステムを解体し、新たな形に変革する必要があります。
製造業における技術を継承するには、属人的な技術に頼らずに運営する必要があります。また、人材不足のため、少人数で運営可能なシステムを構築し、高い品質を持続的に供給できるような生産ラインを目指すことで、競争力を高めることが重要です。
4つメリット
DX推進が工場にもたらすメリットは以下の4つです。
それぞれ解説します。
①データの「見える」化
DXによって可能になるのが、データの「見える」化です。
設備の稼働データを自動で収集・分析することで、故障を予期でき、安全な運営が可能になります。また、製造に関するデータを分析することで、無駄な時間を短縮したり、品質低下の要因を発見でき、生産性の向上と、安定した品質の提供が可能です。
ある工場では、現場の従業員の動きをカメラで検知し、熟練の従業員の動きと比較することで、無駄な動きをなくし、生産性の向上を図る取り組みをしています。
②コストダウン
設備や製造に関するデータを分析することで、現状の課題を発見し改善につなげ、無駄を省くことができます。この省力化・省人化により、必要な場所に人員やコストをかけられるため、費用の削減に繋がります。
③生産性向上
DXによって先進技術を取り入れることで、業務の効率化・自動化を実現し、生産性を大幅に向上できます。安定した生産ラインの確率は利益に直結します。
④品質向上
一部業務の自動化により、人的ミスを減少できます。これにより、安定した品質による持続的な供給が可能です。また、不良品の削減にもつながり、環境にやさしくコスト削減も達成できます。
▶︎DXがもたらすメリットや導入ステップはこちらの記事で解説しています>>
工場でのDX推進における教育方法
DXを推進するためには、運営側と現場側のDX教育が不可欠です。DXの基礎知識から実際の運用まで幅広く知識を持つことで、工場におけるDX推進が円滑になります。
今回はDX推進における教育方法として「セミナー」と「書籍」について紹介します。
セミナー
企業が提供するDXセミナーの中には、製造業に特化したものがあります。対象の業種が絞られており、紹介されるソリューションや開催されるプログラムの内容が業務に直結するため、実践に役立ちます。
今年も多くの企業が製造業におけるDXセミナーをオンラインで開催し、製造業における現状や課題・それらを解決できるDXソリューションを専門家が解説しています。
終了したDXセミナーの中から、現在もオンデマンドで視聴可能な2つを紹介します。
- SCSK株式会社「今から始める製造業DXセミナー」
配信期間:2021年4月1日~2022年3月31日
参加費 :無料(要登録)
主催 :SCSK株式会社
協賛 :エヌビディア合同会社 SB C&S株式会社
- パナソニック株式会社「製造DXセミナー」
配信期間:特になし
参加費 :無料(フルバージョン視聴は要登録)
共催 :パナソニック スマートファクトリーソリューションズ株式会社
アスプローバ株式会社
ウイングアーク1st株式会社
株式会社シムトップス
▶︎DXセミナーについて詳しくはこちらの記事で解説しています>>
書籍
次に、製造業・工場DXに関する書籍を2つ紹介します。
- 天野眞也「製造業DX 入門編」
「製造業DX 入門編」「製造業DX 実践編」「製造業DX カスタマーサクセス編 」の三部作から構成されており、自身のレベルに合わせて選択が可能です。
三冊の内容は以下となります。
入門編 :製造業DXに関する基礎知識を解説
実践編 :製造業DXを実践するための応用編
カスタマーサクセス編:製造業DXの実現を支援する方のための応用編
- 山口俊之「図解入門ビジネス 最新生産工場のDXがよ~くわかる本」
工場という製造現場におけるDXに特化した一冊です。
基礎知識から推進方法まで説明されており、すぐに運営に反映できます。
▶︎DX人材の育成についてはこちらの記事で解説しています>>
工場DXの成功事例4選
今回紹介する工場DXは以下の4つです。
沖電気工業株式会社 「バーチャル・ワンファクトリー」
「バーチャル・ワンファクトリー」 とは、情報通信本部の傘下にある埼玉県本庄市と静岡県沼津市にある2つの工場を仮想的に1つの工場として融合する取り組みです。
- 課題・背景
沖電気工業株式会社では、マスカスタマイゼーションへの対応や、社会変化による需要減に対する危機感から、工場間の横串連携を検討していました。また、各工場で違う製品を生産していますが、一部共通の部品があります。しかし設計部門は各工場に合わせた設計しており、共通の仕様による生産ができないという課題を抱えていました。
- 取組内容
まず、各工場における生産形態の特徴、製造に対する考え方、知見などの情報を整理し、各工場における設計データの受取りを可能にし、設計情報の共通化に踏み出しました。
また、融合する際には、各部門で交流する「部門間融合」、生産状況の見える化で繁閑に合わせて工場間で助け合う「生産融合」、試作生産を他者に依頼せず多品種少量生産の自社工場で行う「試作プロセス融合」、生産管理システム(ERP)の統合する「IT融合」の4段階を中心に推進しました。
各工場におけるデジタル化専門の生産技術人材が少なかった為、プロジェクトごとに各工場から人材を拠出し、自社の研究開発部門とも連携し、全社的に課題解決に取り組んだといいます。
- 成果
2工場の生産高の合計規模を維持しながら効率化を進めたことで、コスト削減や、人材や技術の交流を活発化し、目標としていた共通化を達成したうえに、互いの強みを生かした生産体制の構築できました。
また、工場間の連携することで、昨今の多品種少量生産へのニーズへ対応や、人手不足に備えた工場間の負荷分散など、工場を取り巻く外的要因による変化に対する対応も容易になりました。
三菱電機株式会社 「e-F@ctory」
「e-F@ctory」は工場内で生産情報とITを連携させる仕組みです。工場設備IoTで製造現場の情報を取得し、生産現場に近い場所でリアルタイムにデータを分析・活用できます。
また、ITシステムとの連携でものづくり全体を俯瞰して分析ができ、生産性向上やコスト改善を目指しています。
- 課題・背景
同社では自社で工場における自働化のための機器(FA機器)を製造しており、各機器の連携によってこれまで見逃されてきたデータの分析し、コスト削減や品質向上が狙えると考えました。
- 取組内容
まず、プロジェクトに必要な基本技術の開発から行いました。
具体的には、生産現場データとITシステムの接続や処理するためのFA-IT連携技術や、自動化に必要なロボットやセンサーをまとめて制御し、現場から必要なデータを収集する制御技術、現場における大量データの高速通信や効率的な収集を可能にする産業用ネットワーク技術の3点です。
更には、「e-F@ctory」を複数の自社工場で実施し、課題を発見し解決することで、社外にも提供できるソリューションへ作り上げました。
- 成果
e-F@ctoryへの取り組みによって「e-F@ctory Alliance」発足と「Edgecrossコンソーシアム」への参画に達成しました。
スマートファクトリーにはソフトとハードの広範囲な技術が必要になります。そこで、同社のFA機器分野と、ソフトウェアや機器類を提供する他社が連携するプログラムである「e-F@ctory Alliance」を発足しました。このプログラムによって、現場だけでなくエンジニアリングチェーンにおけるデータとの連携が実現しました。
e-F@ctoryとは、デバイスや、デバイス近くのサーバでデータ処理・分析するエッジコンピューティングなシステムです。そのため既に現場にあるそれぞれの機器や通信規格の違いを超えたデータ収集が容易である必要があります。
「Edgecrossコンソーシアム」に参画したことでエッジコンピューティング領域のオープンソフトウェアプラットフォームを構築が可能となり、互換性のあるサービスの展開が実現しました。
富士通株式会社「ローカル5Gシステム」
同社では、スマートファクトリー実現のため、ネットワーク機器の製造拠点である自社の小山工場において現場作業の自動化や遠隔支援など業務のDXを実現するローカル5Gシステムの運用を開始しました。
運搬作業や組立作業など、業務を行う場所や内容によって、それぞれに適した電波を使い分けています。小山工場で検証を重ね、2021年度内に製造業を営む他者に向けて同様のサービス提供を目指しています。
- 課題・背景
DXに取り組むために5Gは非常に重要です。
また2020年には、企業・自治体が自社施設向けに5Gの周波数免許を取得することで、自在に利用できるローカル5Gが制度化されました。
製造業では従来、高精細映像やセンサーデータなどは伝送の際に膨大なデータ容量を必要とするため、遅延が発生していました。
こうした課題をローカル5Gの導入によって解決でき、リアルタイムで高精度な分析によって生産性の向上や機器の遠隔制御などを実現することが期待されていました。
- 取組内容
同社は主に3つの取り組みを実施しました。まず、作業のトレーニング遠隔支援です。
現場のエッジコンピューティング環境の中で、製品の3Dモデルを作成し、MRデバイスにその3Dモデルと作業指示を投影することで、熟練者や開発者が現場の作業員に対して遠隔で指導・支援ができます。
次に、リアルタイムな作業確認です。高精細カメラで組立の様子を撮影し、その映像をAIが認識し、正しく作業が行われているかを判定します。
また、運搬作業の自動化にも取り組みました。工場内外の施設と、運搬を行う無人搬送車に高精細カメラを搭載し、その映像をエッジコンピューティング環境に伝送しAIが解析します。
これにより、無人搬送車の位置特定と走行制御ができます。
- 成果
ローカル5Gを活用することで作業のトレーニング遠隔支援が可能になり、支援の効率化を実現できます。
また、リアルタイムで作業の分析を行い、判定結果を作業者へリアルタイムにフィードバックすることで、作業ミスの減少に繋がり、検査の省力化や品質向上が可能です。運搬の自動化によって運搬コストの削減にもつながります。
NEC「工場付加価値時間計測ソリューション」
同社では、従業員の動きを撮影した映像から実質稼働時間などを計測し、稼働状況を可視化する「工場付加価値時間計測ソリューション」を開発しました。
- 課題
製造業では、現場から作業が詰まる箇所の特定が求められてきました。しかし、それらを目視で実施することが主流であり、非効率的な現状でした。
また、製造業では生産性向のため、全体に影響を及ぼすような問題を抱える箇所を把握するボトルネックという工程があります。しかし、このボトルネックを担当者が目視で実施し、ひとつひとつストップウォッチで計測していたため、同時並行での測定ができず、結果的にボトルネックがどこにあるのか把握できない現状がありました。
- 取組内容
「工場付加価値時間計測ソリューション」では、上部に設置したカメラが作業の様子を撮影し、作業員の動きを自動で検出します。画面上の枠内に作業員が映ると「稼働」、外れれば「非稼働」と自動で判断して計測を行います。計測したデータによって稼働率や、エリアごとの状況をグラフ化し可視化できます。
- 成果
このシステムによって、これまで人の手によって行われていた作業を自動化することが可能になります。また、ボトルネックが一目で見つかり、人員配置の最適化や従業員の教育が容易になります。同社によると、従来のやり方から時間を半分に短縮できたといいます。
同システムは、他社にも販売が開始され、新たな商材としても活躍しているシステムです。
参照:経済産業省|製造業DX取組事例集
富士通|富士通、自社工場において現場作業の自動化や遠隔支援を行うローカル5Gシステムを運用開始
日本経済新聞「NEC、DXで工場を効率化 作業滞る工程を映像で特定」
DXの成功事例はこちらの記事で30個まとめて詳しく解説しています>>
工場でDX推進を行い、課題解決につなげましょう
いかがでしたでしょうか。少子高齢化や災害など、社会的要因によって工場では新たな課題が生まれています。これらは、DXによって改善や解決が可能です。
ぜひ実施事例を参考に、DX推進を検討してみましょう。